Im Forschungsprojekt NeWiP wurden in den vier Anwendungsszenarien verschiedene Demonstratoren über die Projektlaufzeit aufgebaut. Diese dienten in erster Linie der prototypischen Entwicklung von Anwendungen und Lösungen im Projekt und darüber hinaus für eine Veranschaulichung der Ergebnisse und der Verwendung im Ergebnistransfer. Die nachfolgenden Demonstratoren stehen am ZeMA – Zentrum für Mechatronik und Automatisierungstechnik. In Summe wurden bis zum Projektende vier Einzeldemonstratoren entwickelt. Die vier Demonstratoren aus den Anwendungsszenarien ZF Friedrichshafen AG, Woll Maschinenbau GmbH, Imperial-Werke oHG – ein Unternehmen der Miele Gruppe sowie XENON Automatisierungstechnik GmbH werden nachfolgend vorgestellt.
Weitere Projektinformationen
1. Demonstrator für das Anwendungsszenario ZF Friedrichshafen AG
Problemstellung:
Fehlerhafte Produkte werden nach der Qualitätskontrolle in einem Reparaturbereich überarbeitet. Für die Reparatur stehen Einzelarbeitsplätze zur Verfügung, die Reparatur selbst wird überwiegend manuell durchgeführt. Aufgrund der Komplexität des Produktes, der Variantenvielfalt und zunehmender Kundenanforderungen ergeben sich dadurch folgende Problemstellungen:
– Unzureichende Kontrolle und Dokumentation der durchgeführten Prozesse in der Reparatur
– Schulung und Qualifikation von neuen Mitarbeitern ist überaus zeitintensiv und sehr umfangreich
Im Anwendungsszenario und im Demonstrator wurden daher Lösungen entwickelt, um einerseits eine Prozesskontrolle für die kritischen Prozesse (FMEA) zu realisieren sowie andererseits den Mitarbeiter im Prozess zu assistieren.
Vorteile der Lösung:
Der Einsatz einer bedarfsgerechten Assistenz und Training „on-the-job“ des Mitarbeiters ermöglicht die kontinuierliche Ausbildung und Qualifikation von Mitarbeitern. Auch eine flexible Erstellung des Arbeitsplans, bei zeitgleich variantenabhängigen Prozessabläufen, kann gewährleistet werden. Darüber hinaus ergeben sich Vorteile in der Kundendokumentation, da die verschiedenen eingesetzten Systeme eine Kontrolle und Dokumentation der Reparaturvorgänge ermöglichen.
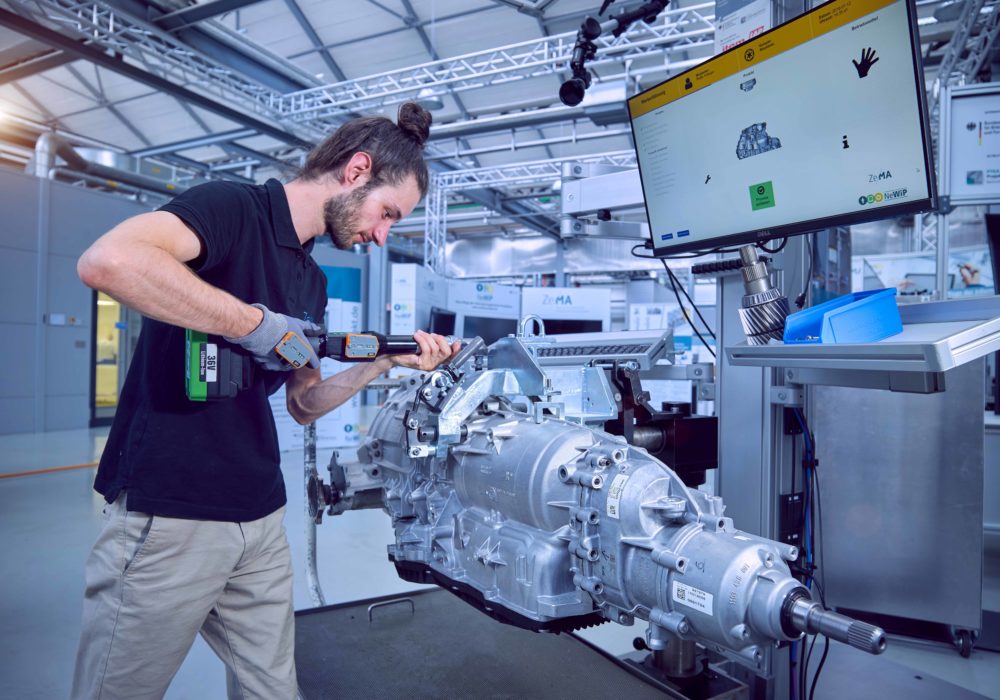
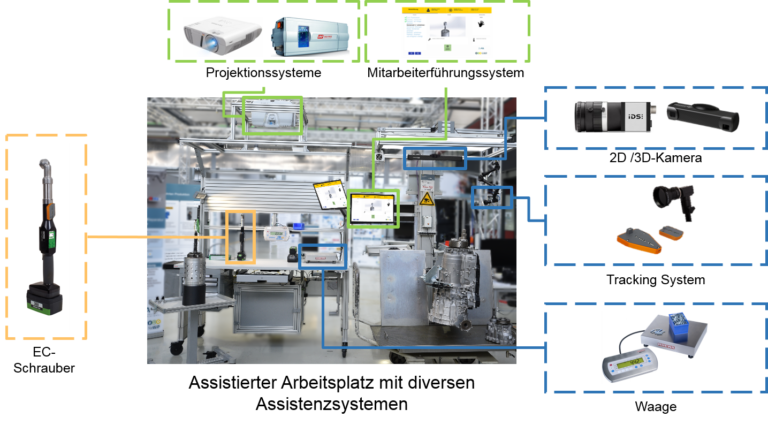
Genutzte Technologien / Entwicklung:
In der Entwicklung wurden unterschiedliche Aspekte eines assistierten Reparaturarbeitsplatzes betrachtet. Diese umfassen Planung und Vorbereitung, Steuerung und Kommunikation, Mitarbeiterassistenz und eingesetzte Sensorik sowie Betriebsmittel.
In der Planung und Vorbereitung können ausgehend von vorhanden Daten und Informationen zu Produkt, Prozess, Betriebsmittel und dem vorliegenden Fehlerfall der Reparaturplan abgeleitet werden. Für die Ableitung des Reparaturplan und Reparaturpfades (Demontage – Reparatur – Montage) wird ein Pathfinding-Algorithmus eingesetzt, der ebenso ein dynamisches „Umplanen“ (bspw. im Falle neuer / weiterer Fehler) ermöglicht.
Für die Kommunikation und Steuerung der einzelnen Systeme wurde MQTT eingesetzt, welches auf Basis des abgeleiteten Reparaturplans das Mitarbeiterassistenzsystem als auch die eingesetzten Sensoren und Betriebsmittel parametrisiert ansteuert.
Das entwickelte Mitarbeiterassistenzsystem besteht insbesondere aus visuellen Systemen. Neben Systemen wie Laserprojektor und Beamer, die den Mitarbeiter mit Hinweisen und wichtigen Informationen im Arbeitsbereich oder am Produkt versorgen, wurde auch ein Mitarbeiterführungs- und Trainingssystem entwickelt, welches den Mitarbeiter mittels Text, Bildern, Animationen und Videos über Prozesse informiert und Prozesswissen vermittelt.
Nachfolgende Abbildung zeigt den Demonstrator sowie eine Übersicht der eingesetzten Sensoren und Betriebsmittel.
2. Demonstrator für das Anwendungsszenario Woll Maschinenbau GmbH
Problemstellung:
Für die Produktion der kundenindividuellen Lösungen im Sondermaschinenbau kommen analoge technische Zeichnungen zum Einsatz, nach deren Vorgabe Einzelteile, Baugruppen und letztendlich die Anlage gefertigt und montiert werden. Die Verwendung analoger technischer Zeichnung ist an sich kein Problem allerdings ergeben sich dadurch Schwierigkeiten, wenn es zu Änderungen an Bauteilen und Baugruppen in der Produktion kommt. Diese werden heute meist handschriftlich auf den technischen Zeichnungen vermerkt, wodurch es einerseits zu Verlust der Information, unkenntlichen Anmerkungen oder andererseits zu Fehlerwiederholungen kommen kann, wenn Änderung infolge der papiergebundenen Weitergabe zu spät oder gar nicht in der Konstruktion erfasst und nachgepflegt werden. Hinzu kommt die Problemstellung der Rückverfolgbarkeit und Kennzeichnung von Materialien und Bauteilen bzw. Baugruppen im Sondermaschinenbau.
Vorteile der Lösung:
Die im spezifischen Anwendungsszenario entwickelte Lösung ermöglicht die digitale und zeitnahe Dokumentation und Kommunikation von Änderungen und behält andererseits die analoge technische Zeichnung im Produktions- oder Baustellenumfeld bei. Die Lösung ist mobil (Tablet, Smart Phone, etc.) einsetzbar und kann daher sowohl im Produktionsumfeld als auch auf Baustellen, etc. eingesetzt werden. Neben verschiedenen Funktionen für die Dokumentation einer Änderung können auch zusätzliche Informationen wie die digitale technische Zeichnung abgerufen werden.
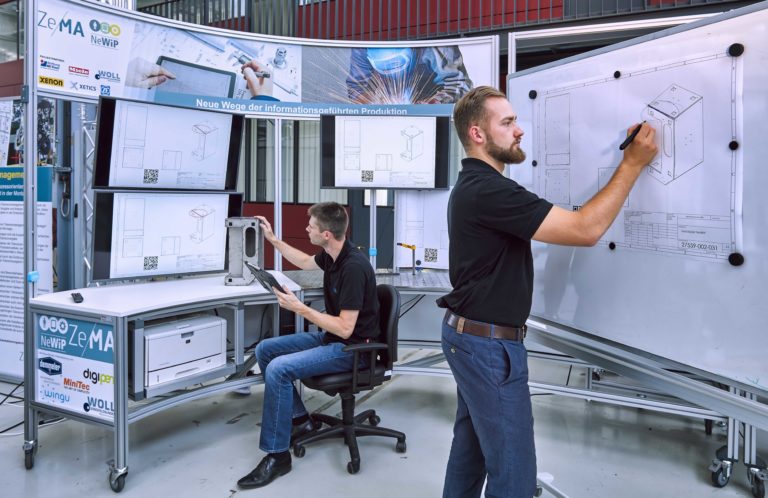
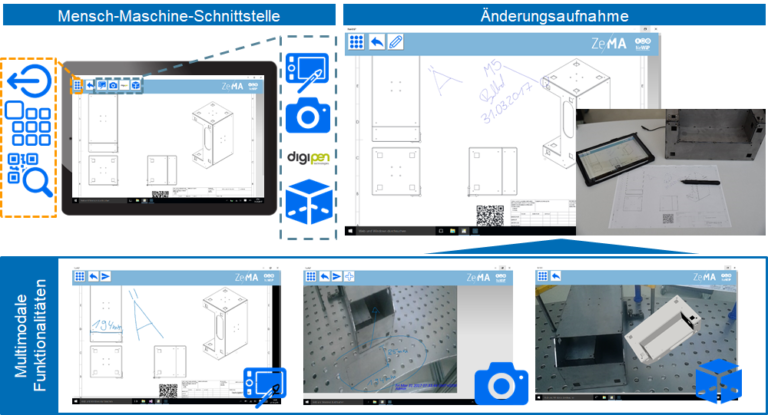
Genutzte Technologien / Entwicklung:
Im Demonstrator werden einerseits die entwickelte Applikation zur Dokumentation von Änderungen und andererseits verschiedene Möglichkeiten der Kennzeichnung von Materialien dargestellt. Die entwickelte Applikation zur Dokumentation von Änderungen ist eine mobile Lösung und kann bspw. auf einem Tablet eingesetzt werden. Für die Konstruktionsabteilung wurden Software-Plugin entwickelt mit deren Hilfe entweder im CAD Programm oder bei der Konvertierung von Zeichnungsdateien in PDF ein Auto-ID-Code (QR oder DMC) auf die technische Zeichnung aufgebracht wird. Dieser ermöglicht eine eindeutige Identifizierung der technischen Zeichnung. Bei der Dokumentation einer Änderung wird der Auto-ID-Code eingescannt und die Informationen zur technischen Zeichnung digital geladen. Dem Mitarbeiter stehen durch die Applikation mehrere Funktionen für die Dokumentation einer Änderung an Bauteil und technischer Zeichnung zur Verfügung. Einerseits kann die Änderung per Tablet-Stift direkt in der digitalen Version vorgenommen werden, andererseits können Fotos vom Sachverhalt gemacht und kommentiert werden. Im Demonstrator steht zusätzlich ein „intelligenter“ Stift zur Verfügung, mit dem der Mitarbeiter Änderungen weiterhin handschriftlich auf der technischen Zeichnung vermerken kann, die aber über eine integrierte Kamera erfasst und ebenfalls direkt digitalisiert werden.
3. Demonstrator für das Anwendungsszenario Imperial – ein Unternehmen der Miele Gruppe
Problemstellung:
Im Anwendungsszenario Imperial des Forschungsprojekts stand das Thema Transparenz in der Produktion im Vordergrund. Betrachtet wurde die Dampfgarerproduktion am Standort Bünde. Im Werk werden in sehr hoher Wertschöpfungstiefe die unterschiedlichen Dampfgarer-Familien und deren Varianten produziert. Abgesehen von einigen spezifischen Punkten in der Produktion (bspw. Prüfung) in der eine automatisierte Rückmeldung der Produkte und Prüfungsergebnisse erfolgt, sind die Planer und Teamleiter im operativen Tagesgeschäft oftmals auf manuelle Rückmeldungen angewiesen. Insbesondere bei ungeplanten Ereignissen sind personalintensive Abstimmungsrunden erforderlich, um den aktuellen Status einschätzen und eine Entscheidung zur Weiterführung der Produktion zu treffen. Im Szenario wurden deshalb die Themen MES, Maschinenanbindung und intelligente Materialwagen verfolgt und Lösungen entwickelt. Der am ZeMA verfügbare Demonstrator umfasst die beiden, im Projekt entwickelten, intelligenten Materialwagen.
Vorteile der Lösung:
Die Materialwagen sind mit verschiedenen Sensoren ausgestattet, die es ermöglichen, den Materialwagen zu identifizieren, zu orten, Informationen und Rückmeldungen zu bekommen als auch die einzelnen Slots des Materialwagens zu überwachen. Insgesamt bietet der Materialwagen so die Möglichkeit kontinuierlich Rückmeldung zum aktuellen Status zu senden, wodurch im MES Details zum Standort und Materialbestand visualisiert werden können. Der Einsatz robuster „Industriesensoren“ ermöglicht den Einsatz der Materialwagen im Fertigungs- und Montageumfeld. Allerdings stehen die heutigen Sensorpreise einem flächendeckenden Einsatz im Weg.
Genutzte Technologien/ Entwicklung:
Im Demonstrator und den beiden intelligenten Materialwagen wurden unterschiedliche Sensoren verbaut, um in der Entwicklung einen Technologieträger für weitere Tests zu schaffen. So verfügen die Materialwagen bspw. für die Bestanderfassung über redundante Systeme (manuelle Erfassung bis vollautomatische Erfassung). Die Materialwagen sind mit Beacons zur Identifikation und zur Lokalisierung mittels RSSI-Wert ausgestattet. E-Ink-Displays ermöglichen die Visualisierung von geladenem Material und zugeordnetem Auftrag direkt am Materialwagen. Zur Erfassung der Bestände im Materialwagen kommen einerseits Funksensoren zum Einsatz als auch UHF-RFID-Technologie. Der Einsatz der UHF-RFID-Technologie in Kombination mit LED ermöglicht zudem die Umsetzung einer Mitarbeiterführung beim Zuführen oder der Entnahme von Material. So können die einzelnen Slots mit LED ausgestattet werden und ein Pick-to-Light realisiert werden. Für die Materialwagen wurde ein Steuerungsprogramm entwickelt, um die unterschiedlichen Technologien miteinander zu verknüpfen und die Daten für die Weitergabe an das im Szenario eingesetzte MES-System von XETICS weiterzugeben. Die Anbindung der Materialwagen an das MES erfolgt dabei über eine REST-API Schnittstelle.
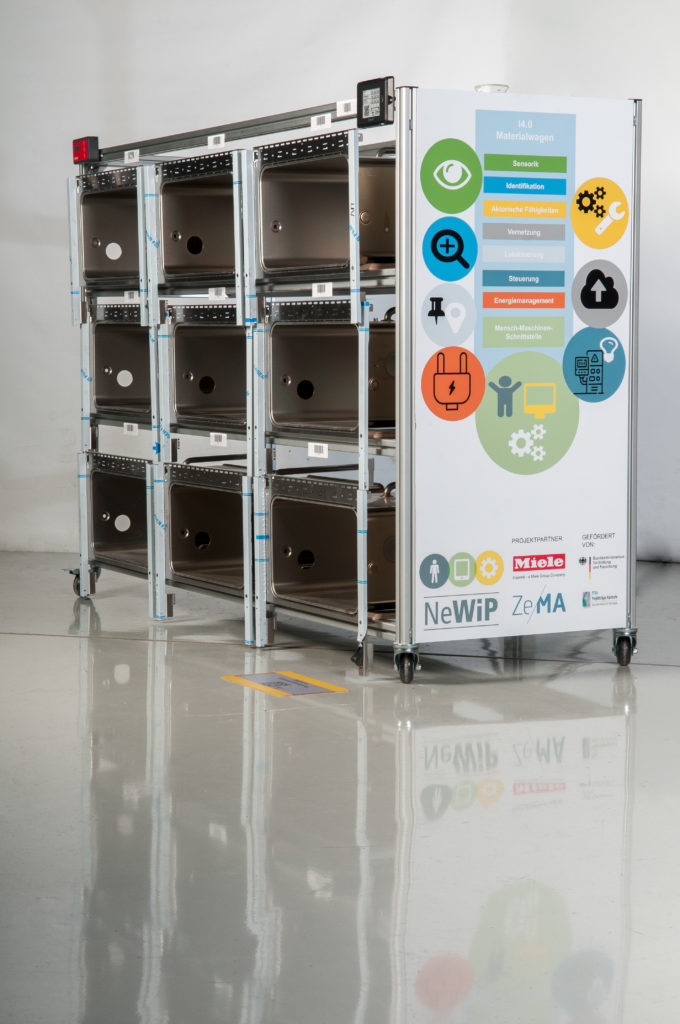
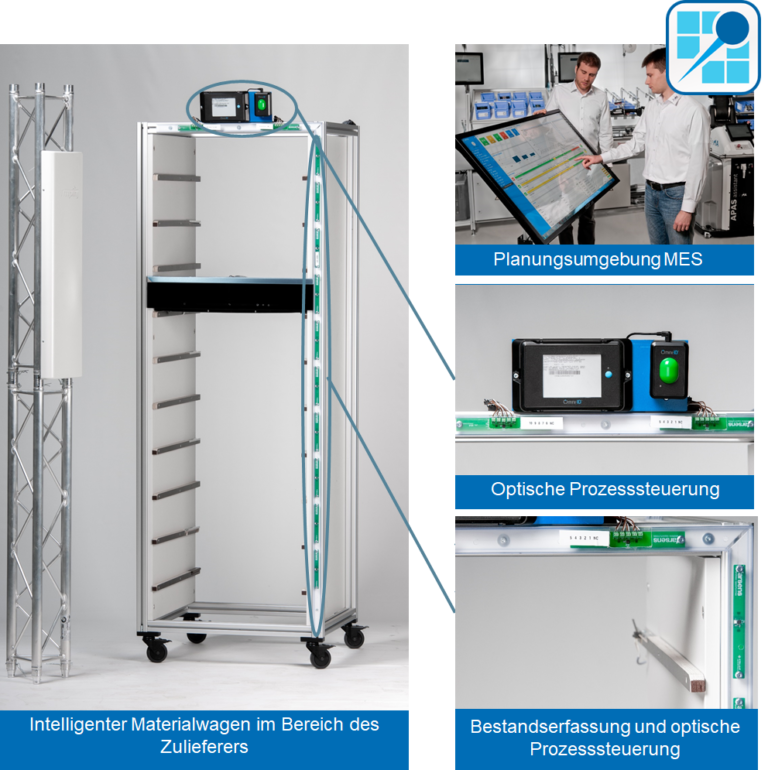
4. Demonstrator für das Anwendungsszenario XENON Automatisierungstechnik GmbH
Problemstellung:
Im Anwendungsszenario XENON stand die Entwicklung von Werkzeugen zur Vernetzung von Experten im Produktionsanlagenbau im Mittelpunkt. XENON entwickelt und produziert Produktionsanlagen nach Kundenvorgaben. Die Abstimmung mit dem Kunden ist zu allen Zeiten ein wichtiger Bestandteil der Projektabwicklung ebenso wie der interne Umgang mit projektrelevanten Daten und Informationen. Für die Phasen Angebotserstellung, Anlagenentstehung und Service ist die Verfügbarkeit von aktuellen Daten sowie die Abschätzung von Auswirkungen infolge von kurzfristigen Änderungen entscheidend. Im Projekt wurden daher Werkzeuge entwickelt, um Planer und Entwickler während der Anlagenentstehungsphase zu unterstützen und die Arbeit mit dem Kunden transparenter zu gestalten; für die Servicephase wurde eine Serviceplattform entwickelt, um Kundenanfragen und Servicetätigkeiten in Abstimmung mit dem Kunden schneller und effizienter umzusetzen.
Vorteile der Lösung:
Die entwickelten Lösungen und Werkzeuge unterstützen die Mitarbeiter, vornehmlich aus dem Bereich Planung und Entwicklung sowie im Service. Durch den Plattform- und Vernetzungscharakter der Lösungen kann sowohl die interne Abstimmung zwischen einzelnen Personen und Teams verbessert als auch externe Experten des Kunden eingebunden werden. Weitere prototypische Werkzeuge unterstützen die Mitarbeiter bspw. bei der Überarbeitung von Lastenheften, dem Abgleich von Änderungen oder Beschreibung von Datensätzen für effizientere Suchen.
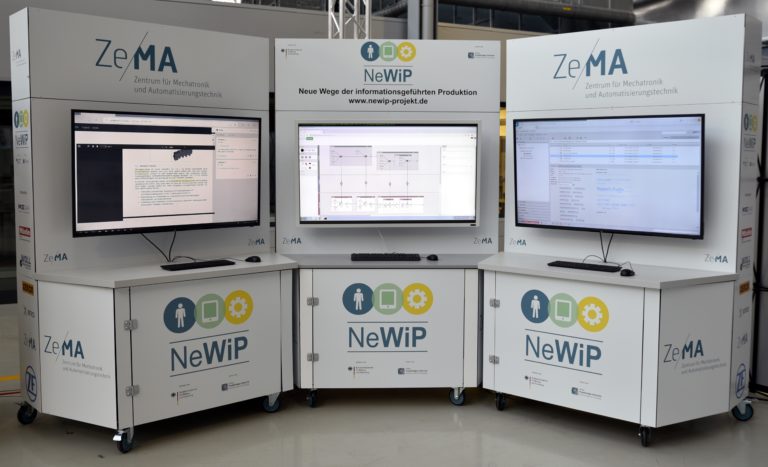
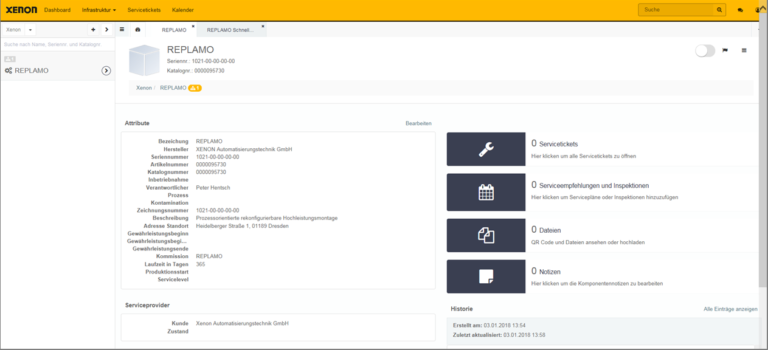
Genutzte Technologien / Entwicklung:
Der im Projekt für das Anwendungsszenario gestaltete Demonstrator zeigt die vornehmlich softwaretechnischen Werkzeuge und deren Funktionen. Im Projekt wurden folgende Werkzeuge entwickelt und prototypisch implementiert:
Lastenheftannotationstool: gemeinsame Bearbeitung und Kommentierung eines Lastenhefts mit verschiedenen Sichten und Gruppen verschiedener Abteilungen, um einen konsistenten Informationsstand aller Beteiligten zu erreichen.
Planungsumgebung: Tool zur Planung von Produkt, Prozess und Betriebsmitteln sowie dem Aufzeigen von Änderungsbedarfen und deren Auswirkungen bei Produkt, Prozess oder Betriebsmitteln. Anwendung einer semantischen Beschreibungssprache.
Dokumentenmanagement: Werkzeug zur semantischen Beschreibung insb. von CAD-Daten mit Metadaten, um eine systematische Kennzeichnung der Daten zu erreichen und darüber hinaus das Auffinden von bereits existierenden CAD Daten im System mittels semantischer Suche zu vereinfachen.
Produktveränderungserkennung: Ausgangpunkt für die Planung einer Produktionsanlage ist das Produkt. Das Tool ermöglicht einen Abgleich von STEP Daten und das Aufzeigen / Hervorheben von Änderungen zwischen zwei Versionen.
Serviceplattform: Entwicklung einer Serviceplattform für die Abwicklung von Kundenanfragen. In der Plattform sind wichtige Informationen zur Anlage, etc. hinterlegt, um einen einfachen Zugriff zu ermöglichen und den Servicemitarbeiter in-house und beim Kunden mit den wichtigsten Details zur Anlage zu versorgen oder die Instandhaltung des Kunden zu unterstützen.
Konsortium
Imperial-Werke oHG – Unternehmen der Miele Gruppe
Miele-Straße 1
32257 Bünde
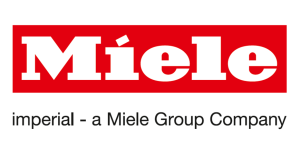
Woll Maschinenbau GmbH
Krughütter Straße 93
66128 Saarbrücken
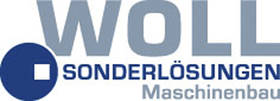
XENON Automatisierungstechnik GmbH
Heidelberger Straße 1
01189 Dresden
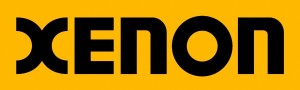
XETICS GmbH
Sigmaringer Straße 121
70567 Stuttgart
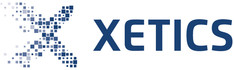
ZF Friedrichshafen AG
Südring
66117 Saarbrücken
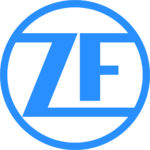
Zentrum für Mechatronik und Automatisierungstechnik gemeinnützige GmbH
Eschberger Weg 46
66121 Saarbrücken
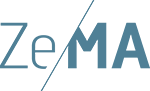
Verband der Metall- und Elektroindustrie des Saarlandes e.V. (ME Saar)
Harthweg 15
66119 Saarbrücken
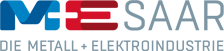
Veröffentlichungen
Abschlussbericht und Veröffentlichung
Müller, R. et al.: NeWiP – Neue Wege der informationsgeführten Produktion. Erschienen in Forschungsberichte Montagetechnik und -organisation, Band 2. ISBN: 978-3-8440-6580-0. Aachen, Shaker-Verlag, 2019.
Vorträge und Veröffentlichungen auf Konferenzen
2017
Müller, R. et al.: Kommunikation im Anlagenentstehungsprozess – Plattform zur Unterstützung der Kommunikation zwischen Kunde und Anlagenbauer. wt Werkstattstechnik Online Jahrgang 107 (2017) H. 9
Müller, R. et al.: Development of a lean information and communication tool to connect and digitize company departments in small and medium-sized enterprises. The thirteenth International Conference on Autonomous Systems, Barcelona, 2017.
Müller, R. et al.: Menschzentriertes Informationstool zur innerbetrieblichen Vernetzung. Mensch und Computer, Regensburg, 2017.
Müller, R. et al.: Lean information and communication tool to connect shop and top floor in small and medium-sized enterprises. 27th International Conference on Flexible Automation and Intelligent Manufacturing, Modena, 2017.
Müller, R.: Consistent provision of information through cyber-physical systems at an assembly machine manufacturer. 67th CIRP General Assembly, Lugano, 2017
Müller, R. et al.: Werkerführung verteilt Infos. Handling, Heft 1-2, Hg. v. Born, P., WEKA Business Medien GmbH, 2017, S. 50-51
2018
Müller, R. et al.: Towards an integrated knowledge management system for small and medium-sized enterprises in the field of assembly system engineering. eKNOW 2018 The Tenth International Conference on Information, Process, and Knowledge Management, Rom, 2018.
Müller, R. et al.: Communication and knowledge management platform for concurrent product and assembly system development. 7th International conference on Changeable, Agile, Reconfigurable and Virtual Production (CARV2018), Nantes, 2018.
Müller, R. et al.: Industrie 4.0-Baukasten zur Digitalisierung von Produktionsprozessen am Beispiel eines vernetzten Materialwagens. 27. Deutscher Materialfluss-Kongress, München, 2018.
Müller, R. et al.: Development of an intelligent material shuttle to digitize and connect production areas with the production process planning department. 51th CIRP Conference on Manufacturing Systems, Stockholm, 2018.
Müller, R. et al.: Information and data structure to create flexible work plans for worker assistance system used at rework site. Procedia CIRP, Band 79, Hg. v. Teti, R.; D’addona, D.M., CIRP, S.147-152, Neapel, 2018.
Müller, R. et al.: Worker centered cognitive assistance for dynamically created repairing jobs in rework area. Procedia CIRP, Band 72, Hg. v. Wang, L., CIRP 2018, S. 141-146
Möhwald, H. et al.: Industrie 4.0 – Mitarbeiter einbinden. Fallbeispiele aus der betrieblichen Praxis. Hrsg. Arbeitsgruppe „Industrie 4.0 – Mitarbeiter einbinden“, Leipzig, 2018.
2019
Müller, R. et al.: Simulation-based Online Production Planning. 29th International Conference on Flexible Automation and Intelligent Manufacturing, Limerick, 2019.
Müller, R. et al.: Einführung von Cyber-Physischen Systemen zur Online-Planung/Steuerung von Produktionsprozessen bei einem KMU. wt Werkstattstechnik Online Jahrgang 109 (2019) H. 4
Müller, R. et al.: Befähigung von Bestandsanlagen und -maschinen zur unternehmensübergreifenden Vernetzung. Mittelstand-Digital Magazin „Wissenschaft trifft Praxis“ Ausgabe 12, 2019.
Müller, R. et al.: Networking of top- and shop floor by a lean information communication tool to control and optimise production processes. 52nd CIRP Manufacturing Systems Conference, Ljubljana, 2019.
Müller, R. et al.: Intelligent and flexible worker assistance systems – assembly assistance platform for planning assisted assembly and rework as well as execution of a worker-centered assistance. Proceedings of the 13th International Joint Conference on Computer Vision, Imaging and Computer Graphics Theory and Applications (VISIGRAPP 2018), Band 2, Hg. v. Richar, P.; Chessa, M.; Braz, J., Insticc, Funchal, 2019
Müller, R.: Cognitive worker assistance for dynamically created repairing jobs in the rework area. 68th CIRP General Assembly, Tokyo, 2019.
Müller, R. et al.: Situational cognitive assistance system in rework area. 29th International Conference on Flexible Automation and Intelligent Manufacturing, Limerick, 2019.
Vorträge auf Fachtagungen und Industriearbeitskreis
Müller, R.: Neue Wege der informationsgeführten Produktion – Strategien, Vorgehensweisen, Anwendungsszenarien. 9. Montage-Tagung, Saarbrücken, 2017.
Schmitt, K-J.; Burkhard, D.: Menschzentriertes Informationstool zur innerbetrieblichen Vernetzung. Industriearbeitskreis „Zukunftsstabile Montage“ Bosch Rexroth. Stuttgart, 2017.
Schmitt, K-J.; Burkhard, D.: Vernetzung der innerbetrieblichen Wertschöpfungskette, eine bedarfs- und anforderungsgerechte Digitalisierung von Shop- und Top-Floor bei einem KMU. Mittelstandszentrum 4.0, Saarbrücken, 2017.
Vierfuß, R.; Ahmadi, A.; Burkhard, D.: Agile Produktionssysteme zur online-Planung und –Steuerung durch die Digitalisierung der Wertschöpfungskette bei der Firma Imperial-Werke oHG. VDMA Abschlussveranstaltung Verbundprojekte. Frankfurt, 2018
Burkhard, D.: Digitalisierung bestehender Fertigungsanlagen und -maschinen. Mittelstand 4.0-Kompetenzzentrum, Saarbrücken, 2018
Burkhard, D.: Durch Produktionsvernetzung die Effizienz steigern – Einführung in die Produktionsvernetzung in verschiedenen Unternehmensbereichen. Mittelstandszentrum 4.0, Saarwellingen, 2018
Müller, R.: Neue Wege der informationsgeführten Produktion – Beispiel und Anwendung. 11. Montage-Tagung, Saarbrücken, 2019.