Verteilte Produktion für die saarländische Automotivindustrie: Nachhaltig, Vernetzt, Resilient
Problemstellung
Zielsetzung
• Standardisierung von Schnittstellen, Datenaustauschformaten und Semantiken zum vereinfachten Datenaustausch und Datenverständnis
• Kommunikation und Vernetzung von Produktionsressourcen zur automatischen horizontalen und vertikalen Informationsübermittlung
• Betriebs- und Angriffssicherheit der kommunizierenden Produktionsressourcen
• Wandlungsfähigkeit und Resilienz von Produktionsressourcen (mit der Betrachtung von Robotersystemen als häufige Komponente in der Prozessautomatisierung)
• Umgang und Organisation von veränderten Produktionssystemstrukturen und Kompetenzprofilen der Mitarbeiter
• Modellierung von Teil- und Gesamtsystemen zur Sicherstellung von Transparenz und zur Identifikation von Optimierungspotentialen
Vorgehen
Dabei werden, bezogen auf die jeweiligen Arbeitspakete, folgenden Schwerpunkte adressiert:
1. Konzeption und Abgrenzung fundamentaler Systembausteine: Auswahl und Definition von Standards sowie Konzepten zum kontrollierten Zugriff auf alle Informationen eines Assets der Produktion (Produkt-, Prozess- und Betriebsmitteldaten) - vergleichbar mit einer Verwaltungsschale (AP1)
2. Produktentstehung/Fertigung: Entwicklung eines Expertensystems zur Mitarbeiterunterstützung bei der Parametrisierung neuartiger Fertigungsprozesse (AP2)
3. Agile adaptive Produktionsressourcen: Entwicklung einer agilen, adaptiven Ressource auf Basis smarter Materialien zur direkten Unterstützung des Mitarbeiters auf Shop Floor Ebene und Gewährleistung des Datenflusses zwischen realen und digitalen Komponenten (Asset) (AP3)
4. Adaptive Robotik: Entwicklung und Implementierung von konventionellen und lernenden Ansätzen zur simulativen Untersuchung (Kollisionsuntersuchungen, Erreichbarkeitsprüfungen, Bahnplanung) bestehender intelligenter Roboter-Systeme zur digitalen Verifikation und Übertragung in die reale Produktionsumgebung (AP4)
5. Planung & Optimierung: Fähigkeitsabgleich zwischen sich ändernden Produktspezifikationen und betrieblichen Ressourcen zur Durchführung simulationsgetriebener Optimierungsstrategien (AP5)
6. Produktionssystemorchestrierung: Entwicklung eines Software-Systems (hochflexibles Manufacturing Execution System, MES) zur Orchestrierung von Produktionsressourcen (AP6)
7. Multisensorsystem & Datenfusion: Entwicklung eines übergreifenden Ansatzes zur prädiktiven Analyse von Verschleißteilen am Produktionssystem und Anreicherung des digitalen Zwillings mit relevanten Schlussfolgerungen (AP7)
8. Industrial Security: Anreicherung des entwickelten Digitalen Zwillings mit relevanten Security-Informationen und Entwicklung von automatisierten Security Checks auf Basis dieser Informationen (AP8)
9. Projektmanagement und Umsetzung in einem Demonstrator: Aufbau eines physischen Demonstrators mit softwarebasierten Modulen zur Realisierung einer verteilten Produktion am ZeMA (AP9)
Verwertungskonzept
Weiter kann der Demonstrator für die Lehre und für Weiterbildungsmaßnahmen verstärkt eingesetzt werden. Es bieten sich beispielsweise Schulungen und Seminare im Bereich der vernetzten Produktion, Aufbau Digitaler Zwillinge, Datensicherheit und -qualität an sowie weiterführende Forschungsvorhaben zu Themen der virtuellen Anlageninbetriebnahme sowie des energieeffizienten Betreibens von Anlagen an, etc. Zudem können in Kooperation beispielsweise mit dem automobilen Netzwerk Saarland Angebote erarbeitet werden. Letztlich können die hier erarbeiteten Ergebnisse direkt im Kontext von Transferprojekten nutzbar gemacht werden. Im Rahmen derzeitiger Projekte und deren Nachfolgerprojekten (KomZetSaar - Mittelstand-4.0 Kompetenzzentrum, RZzKI - Regionale Zukunftszentrum für KI und digitale Transformation, können wissenschaftlich erarbeitete Erkenntnisse direkt mit regionalen Unternehmen, im speziellen KMU geteilt werden.
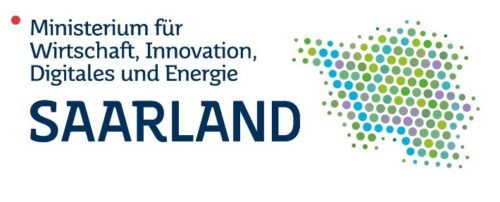
Projektleitung: Max Eichenwald, M.Sc.
Laufzeit: 01.10.2022– 30.09.2026
Gefördert von: EU (EFRE), Staatskanzlei des Saarlandes
Ministerium für Wirtschaft, Innovation, Digitales und Energie